Delivering on a promise of reliability Crisplant helps Parcel/Direct hit the bull's-eye
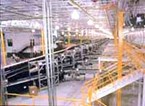
Contents:
Primed and ready to go
Surveying the field, making a pick
Doing the numbers
More than just material-handling muscle
When Quad/Graphics of Pewaukee, Wisconsin, announced its launch of Parcel/Direct into the parcel-delivery field in September 1997, the company viewed Parcel/Direct as a practical extension of its services.
Already an industry leader in mail consolidation and distribution, Quad/Graphics was shipping 12 million pounds of magazines and catalogs a week to U.S. Postal Service facilities across the country. The addition of parcel delivery for mail-order and e-commerce businesses was seen as a natural progression.
But while the creation of Parcel/Direct may have been a practical extension, it was hardly an inexpensive one. It cost an estimated $26 million to launch Parcel/Direct and inherit the privilege of competing directly with delivery-juggernauts FedEx and United Parcel Service (UPS). Add to the mix the increased demand for speed and convenience to meet promises of consistent delivery, and Parcel/Direct's margin for error was thinner than an eggshell.
Primed and ready to go
Parcel/Direct had plenty in its arsenal. Partnering with the U.S. Postal Service, Parcel/Direct offered more competitive pricing than UPS or FedEx, and the company boasted tracking of packages by global-positioning technology, which allowed tracking of orders before they reached a check-in station.
Still, to remain competitive, Parcel/Direct knew it would have to be more than just a better value. It would need to be reliable, quick and accurate. In the end, Parcel/Direct's technology would make or break the company.
Here's how Steve Zwieg, Parcel/Direct's vice president of development, put it: "We sought speed and accuracy in the sortation process. When a customer is told that they will receive their order in three to seven days, it's our responsibility to make sure that happens. So we knew we needed to install technology that would provide reliable service to the client."
Back to top
Surveying the field, making a pick
After meeting with five companies specializing in sortation technology, Parcel/Direct chose Crisplant Inc. of Frederick, Maryland, to supply sortation systems to its two processing facilities in New Berlin, Wisconsin (where Parcel/Direct is headquartered), and Martinsburg, West Virginia.
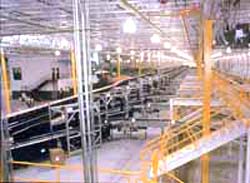
center in Martinsburg, West Virginia, can handle
more than 150,000 parcels a day.
Crisplant Inc., an FKI Logistex company, designs and manufactures advanced sortation systems. To date, Crisplant has installed more than 600 tailor-made systems worldwide. The company has locations in the United States, France, Germany and China.
"We had talked to several companies about sortation equipment. Crisplant came to the table with the greatest number of ideas," Zwieg said. "They understood what our sales needs were. They knew where we were starting from, but they also knew that we wanted room to expand our business."
Crisplant was integral in starting up the megaplant in Martinsburg, which has immediate distribution access to 60 percent of the U.S. population. Besides supplying sortation equipment for this facility, Crisplant was charged with managing induction and installation of all the facility's sortation systems, conveyors and scanning technology.
Parcel/Direct is able to offer lower costs because of something called zone skipping, a delivery method in which the Postal Service receives packages closer to their final destination. In fact, Parcel/Direct plans to sort more than half the material shipped through the company to the five-digit destination post office.
This offers two benefits to mail-order companies: first, because merchandise is handled only minimally by the Postal Service, delivery costs fall; and second, because the merchandise is rarely touched, chances that something will be damaged also decrease. But to achieve these benefits, any sorting system inducted had to be accurate, fast and versatile.
Back to top
Doing the numbers
Parcel/Direct's processing plants were built with ease of use, volume and speed of access in mind. The 400,000-square-foot Martinsburg plant was built with dock doors on three sides of the building, allowing trucks to pick up packages from either side for smooth traffic flow. After assessing Parcel/Direct's needs, Crisplant installed the S-2000 tilt tray sorter, one of the industry's most versatile sorters.
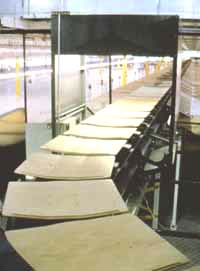
tilt-tray sorters in the Parcel/Direct
Martinsburg, West Virginia, plant.
In all, the tracks have a combined
1,600 trays for sorting parcels.
Made up of interconnected carts driven by linear motors, the S-2000 centers around a wood tray that discharges cargo by tilting to either side. Items are discharged by sliding off the tray at a controlled speed. The tilting mechanism is centered around a tilting arm capped off by a wheel that, at the proper time, feeds into a molded shifting device. The gradual slope of the shifting device allows the tray to move slowly, discharging the tray's cargo with minimal disruption.
The sorter was viewed as perfect for Parcel/Direct, because it can handle light and heavy items, up to 35 pounds. The S-2000 handles any of the items Parcel/Direct normally ships, everything from clothing to upscale kitchen products to the soap of the month.
"We knew the tilt tray sorter would be perfect for what we wanted," Zwieg said. "It gave us the flexibility we needed."
Parcel/Direct also appreciated the speed of the sorter, with trays that move along the track at nearly 2 meters per second. Because of the sorter's configuration, more than 19,500 trays worth of product can be processed in an hour. In a 20-hour operating day, the system can handle 300,000 parcels.
"At any one time, our plant is handling packages from 30 or 40 clients, each of them producing between 500 to 25,000 parcels a day," Zwieg said. "We needed a machine that can handle all of that with speed and accuracy."
Given the high volume of business set to flow through the Martinsburg plant, the tilt-tray sorter was also chosen for maintenance ease. The tilting mechanism is composed of an injection-molded device mounted on top of each tray. The number of moving parts on the mechanism has been kept to a minimum to ensure high reliability. The machine frame that encases the track has removable top and bottom covers, granting easy access for maintenance and inspection.
For Martinsburg, Crisplant installed two tracks of tilt-tray sorters. The primary system is more than 1,600 feet long and contains 700 sorting trays. The secondary system measures 2,100 feet, with more than 900 trays. These sorters have handled up to 150,000 parcels in a day from mail order and e-commerce operations. Besides the sorting system, Crisplant researched, obtained and installed 11 barcode-reading scanners, along with 13,000 feet of conveyor belts.
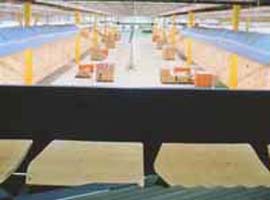
side, discharging the cargo at a controlled speed.
The trays can move at nearly two meters a second
and can process more than 19,500 trays worth of
product an hour.
To ensure zone skipping, parcels brought into the Martinsburg plant are sent through an initial phalanx of scanners. This induction scan determines the height, length and width of a parcel and its destination ZIP code. The parcel is then weighed, so before a parcel even touches the Crisplant sorter, a package's weight, volume and destination are known.
Once scanned, the primary sorter then selects packages from the busiest 4,000 ZIP codes out of the estimated 30,000 to which Parcel/Direct delivers. This so-called busy group entails more than half of the packages sent through Parcel/Direct. The other packages are sent directly to the U.S. Postal Service bulk-mail centers.
Packages from the top 4,000 ZIP codes move on to the larger second sorter, where they're sent down one of 500 chutes and are pushed onto the plant's two and a half miles of conveyor belts.
To expedite the transfer of items into the plant, Crisplant brought in special conveyors to transport parcels from the Parcel/Direct trucks to the tilt trays. Crisplant installed seven telescoping conveyors, which can extend 50 feet from the back of trucks into the plant. Plans are in the works to double the number of telescoping conveyor belts from seven to 14 by the fall.
When it came to shipping parcels after sortation, Crisplant coordinated installation of 36 powered truck-loader conveyors. Sized between 60 and 70 feet long, the loaders can be considered conveyor belts on wheels. Instead of being riveted to the floor, the base of the conveyor is equipped with wheels that can transport the conveyor into the delivery-truck bays.
Due to the extra automation, the Martinsburg plant was able to run with 150 workers, 50 fewer than the New Berlin plant, even though they both handled the same volume.
Back to top
More than just material-handling muscle
Besides installing a system that would move material goods, Crisplant had to transfer millions of bits of information from the Martinsburg plant to the World Wide Web. The information gathered by scanners daily had to be easily accessible to Parcel/Direct's clients via a secure location on Parcel/Direct's Web site. Crisplant worked with Parcel/Direct's software technicians to ensure that the information was available.
Since Parcel/Direct's launch in 1997, the company has grown exponentially, from handling roughly 20,000 packages a day three years ago to nearly 300,000.
Zwieg said he's happy with Crisplant's products and service.
"One of the biggest benefits we find with working with Crisplant is that they're always there," he said. "More than once, we needed to make some adjustments to the system to handle a special number of orders — we have such a diverse range of clientele, that isn't unusual — and Crisplant didn't hesitate to fly people in from their facilities in Denmark or Frederick (Maryland). They've been very responsive to our needs."
So responsive, in fact, that Zwieg has recommended Crisplant to some of Parcel/Direct's larger clients that are looking for sortation systems. And Zwieg hopes to use Crisplant again.
"When we set up a new facility, we will certainly discuss working with Crisplant," he said.
Edited by Michael Lear-Olimpi, Managing Editor, Logistics Online
Source: Crisplant Inc.