ASRS Aisle-Changing Cranes Streamline High-Bay Operation
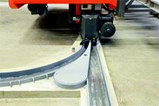
By Patrick Roberts
The latest technology in aisle-changing automated storage and retrieval cranes, like those from LTW Intralogistics, provide significant advantages compared to using dedicated-aisle cranes in high-bay warehouses – such as reducing capital investment and maintenance downtime, while increasing system uptime in handling unit loads and delivering a more cost-efficient ROI for the high-bay’s overall operation.
Automated storage and retrieval systems (ASRS) are computer controlled material handling machines for automatically depositing, storing and retrieving unit loads from defined storage locations. Central to the ASRS is its stacker cranes which permit full-pallet load and layered-pallet inventory to be moved quickly, safely and precisely within a high-bay warehouse environment.
Stacker cranes offer reliability and accuracy that exceed the capabilities of fork lift trucks or turret trucks. Modern cranes operate within a set of top and bottom rails, eliminating the need for any flat-floor requirements.
Since the crane is stabilized by the rail connections, greater load capacities are available, as well as higher rack heights, when compared to free roaming lift trucks.
ASRS cranes have a high efficiency of cycle time, a calculation of the movement of product within a DC’s storage system. Many manual operations in a warehouse transport product in only one direction, then return with an empty load. Stacker cranes place a load into a rack position, and then retrieve a load from storage on their way back out, optimizing the crane’s movements.
The ASRS stacker crane concept has proven itself to be a viable method to reduce operating and distribution costs in the warehouse. Semi-automated and fully-automated cranes reduce the number of people required to operate the warehouse. By incorporating stacker crane systems, a distribution center’s throughput can operate at a more cost-efficient level.
Flexibility, Efficiency Define the Most Advanced Crane Systems ASRS cranes have advanced to an extremely high level of performance, and continue to improve. The latest generation of cranes incorporate a unique flexibility, allowing single-deep, double-deep, triple-deep and up to 20-deep pallet stacking utilizing telescopic forks and shuttle cars, with the flexibility to handle one load at a time or multiple loads.
Such cranes can exceed 140 feet in height carrying payloads of 11,000 pounds, traveling at vertical speeds of 325 feet-per-minute (FPM) and achieving horizontal travel speeds of 787 FPM.
Most can operate in a wide sphere of temperatures, ranging from minus 38° F to 140° F, equipped with wiring, electrical cables and photo-electronic sensors that are designed to withstand these extreme environments.
High-speed PLCs with integrated controls architecture monitor the movements of the cranes. Receiving directions from the distribution center’s warehouse management system (WMS) and warehouse control system (WCS) via Ethernet, the cranes utilize barcode technology to direct their movement in the high-bay and the crane’s movement of pallets.
The most efficient stacker cranes that provide the lowest operating cost per hour are now fully A/C powered. This eliminates the costs associated with DC batteries, charging, and associated maintenance. Such cranes have also eliminated hydraulics, which greatly reduces maintenance costs.
And then there is the power-saving technology designed into some of these cranes – the process of capturing and reusing electricity. As the crane carriage lowers, software allows the power to be captured from the lifting motor, which now becomes the generator. That captured power can be put into a grid inside the distribution center to help power other equipment like conveyor systems or other stacker cranes.
These progressive developmental improvements in stacker crane operation have made them one of the most efficient material handling systems in highly-automated warehouses.
Streamlined Aisle-Changing Functionality Now, aisle-changing functionality has pushed stacker crane operation to an even higher level of efficiency. Although aisle-changing capability in stacker cranes has been around in some form since the early 1990’s, the speed and efficiency with which these new cranes can now execute aisle changes makes them a serious option for use in any DC interested in reducing operational costs while improving throughput.
Most high rise warehouses use ASRS cranes that are only capable of travelling in a straight line, in one aisle. The limitation of such a dedicated-aisle crane is that one crane is required to service each storage aisle in a warehouse. As cranes are a major part of the cost of high-bay warehouse solutions, by reducing the numbers of cranes significant savings can be realized. The number of stacker cranes can be matched to the warehouse throughput instead of to the number of aisles, therefore reducing the capital investment.
Unlike earlier models of aisle-changing cranes which had limitations in their aisle-changing flexibility, some of the latest stacker cranes have been designed with efficient aisle-changing capabilities. One such crane is produced by LTW Intralogistics, a manufacturer of stacker cranes for warehousing. When the LTW crane gets to the end of an aisle, it can then travel perpendicular to the aisle and enter another aisle to continue storing and retrieving pallets.
The crane literally smoothly rotates around the end of the aisle on a curved track, without leaving the track. It makes for an easy and fast transition between aisles. LTW has designed and patented a specialized track to facilitate the move, which requires no transfer mechanisms, supervision equipment or costly and time-consuming maintenance, problems that have plagued earlier aisle-changing cranes.
The ability to switch aisles increases redundancy, in the event that a crane would go out of service. Each pallet position then becomes 100 percent accessible. This also allows cranes to be easily moved off line when service is required into an off-line maintenance area.
If an ASRS solution in place in a distribution facility has ten aisles and is employing ten stacker cranes each operating in its respective aisle, if a stacker crane breaks down there is no way to get products out of that aisle.
With aisle-changing cranes operating in a situation like this, the DC operator could easily move the disabled crane to the maintenance area and the remaining cranes could complete the tasks required in that aisle. The redundancy system would assure that the pallets are retrieved. This is very important to maintaining a high level of delivery assurance.
These new aisle-changing applications require fewer cranes and less capital investment than solutions using fixed-aisle cranes. It is not uncommon for a distribution center with 24 aisles with 50,000 pallets to have just six state-of-the-art aisle-changing cranes servicing them. As the DC’s volume increases, it can add on more stacker cranes to accommodate the need, making the system quite scalable.
Depending on the throughput flow of a distribution center, the DC may employ a combination of dedicated-aisle cranes for aisles with higher volume throughput requirements, and use aisle-changing cranes for those aisles where the volumes are less.
Keeping Throughput on the Move
The most streamlined warehouses today are highly automated facilities, with maximized high-bay, high-density storage utilizing ASRS. These ASRS, in conjunction with the warehouse management system, maintain precision product identification and rotation, provide rapid throughput with over 99.9 percent accuracy levels, and are considerably more energy efficient than their manually-operated facilities.
To stay competitive, distribution centers need to implement systems that will have the flexibility to adjust very quickly and accurately to market conditions such as increases in SKU range and shortened lead times. Keeping throughput on the move is critical in any distribution center. It is here where the latest technology in ASRS aisle-changing functionality can provide the biggest benefit to a company’s distribution effort.
About LTW Intralogistics
LTW Intralogistics manufacturers automatic and manually-operated stacker cranes, and delivers components for high bay warehouse systems including racking, conveyors and warehouse management software. The company also provides engineering and project management for turnkey warehouse solutions.
LTW has delivered hundreds of installations worldwide, and is recognized as the world leader in handling unique loads ranging from 20 lbs. to 20,000 lbs. within fully-automated warehouses.
For more information, visit www.ltwusa.com.
SOURCE: LTW Intralogistics