Komplett's Showpiece Distribution Center For Internet Retailing
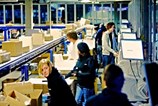
Scandinavia's leading Internet retailer, Komplett ASA, shows how to optimize distribution with its recently upgraded 270,000 square-foot distribution center in Sandefjord, Norway. A showpiece of state-of-the-art logistics technology, with system integration, the DC's central focus is AutoStore, one of the industry's latest and most efficient high-speed systems for automated storage and picking of small goods.
By Jim McMahon
For the largest online retailer in Scandinavia, Komplett's inventory capacity, accuracy of order fulfillment and speed of order processing are critical to maintaining its high-profile market position. In 2010, the computer products and consumer electronics retailer posted sales of more than $700 million, while servicing 675,000 active online customers. So when Komplett decided to expand its distribution center to better service its clients, it leveraged one of the most streamlined automated material handling technologies available, AutoStore®, for the storage and fulfillment of its products. The end result is a distribution center providing a super-streamlined capability for order processing and throughput flexibility – a DC that stands as a hallmark of Internet retail distribution at its best.
The Need for a More Efficient DC
Komplett ASA is a leading player in e-commerce delivering PC components, PCs and other related electronic equipment to consumers and companies throughout Norway, Sweden and Denmark. Founded in 1996, the company has grown to host nine separate webshops, some of which rank as the first and second largest e-commerce sites in Scandinavia. Komplett aims to be the single link between manufacturers and its customers, which include end-users, businesses, public enterprises and resellers.
From its 270,000 square-foot central distribution center in Sandefjord, Norway, the company fulfills all of its orders and ships to its customers throughout Scandinavia. In 2010, Komplett prepared and shipped 1.4 million orders, nearly 4.3 million items.
But these production volumes represent throughput after the company's move to an automated distribution center. For more than a decade prior, Komplett fulfilled its orders manually. Floor trucks moving pallets into storage racks, and case-picking where workers would receive orders from the company's ERP line-by-line, then pick using hand-held RF scanners with products being picked one-by-one. No pick-to-light or pick-to-voice, minimal conveyors and little sortation equipment. Basically, traditional warehouse manual operations.
This system was workable for the company for a decade or so, but as Komplett continued to expand its market reach by acquiring and building new webshops, and increasing its product offerings to more than 10,000 SKUs the need for a more streamlined and automated solution had reached a critical level.
"We needed to make a change to our DC operations for a number of reasons," says Pal Asbjorn Vindegg, Chief Operating Officer for Komplett. "More efficiency was one of the drivers, our manual operation was just not able to keep up with the order volumes any longer. But we also needed more space for storage for our increasing number of products, especially for small products."
"We looked at a number of options," continues Vindegg. "We needed more storage space, but we could not extend the warehouse, and that alone would not improve our efficiency. We were convinced that we needed some kind of automation to handle our storage requirements and streamline our throughput."
"Mini-loads were an option we explored," Vindegg says. "But a mini-load was very difficult to fit into our existing DC because we would have needed more height in the building. Also, we had concerns that if one of the mini-load cranes were to stop, then we would not able to reach the locations connected to that crane."
Optimizing Storage, Streamlining Fulfillment
After considering a variety of solutions, the decision was made to select AutoStore as the central system for the distribution center's automated storage and fulfillment operation. The AutoStore system is designed for operators that require both dense storage and efficient piece- and small-case picking, exactly what Komplett needed. Element Logic AS, a local integrator in Norway, installed Komplett's AutoStore system. Swisslog is the exclusive distributor of AutoStore in North America. It also distributes the system in much of Europe. AutoStore is a registered trademark of Jakob Hatteland Logistics AS, and manufactured by the company in Norway.
AutoStore is made up of a three-dimensional grid of self-supporting bins that are moved to pick stations by independently-operating robots. Each robot has two sets of wheels that enable it to move along two axis. This makes it possible for all robots to reach any position on the grid. The robots are equipped with a lift for picking up, carrying and putting Komplett's 33,000 bins that are stored in the grid. They communicate via wireless controls to the WMS and Komplett's pick stations.
The system stores goods with minimum space requirements. With no room necessary for forklifts, roads or ramps it uses the available storage space to the maximum. It stores up to 60 percent more goods per cubic foot than conventional warehouse systems.
A key capability of the AutoStore system is that it provides exceptional flexibility, and can be adapted and expanded as needed. For example, Komplett's installation could easily be extended, if the need warrants in the future, without interfering with its throughput. Additional storage space can be added by simply extending the grid. Additionally, pick rates can be enhanced by adding more robots to the system. Currently, Komplett is running 55 robots, having already increased the number of robots twice since AutoStore was installed.
"The strength of AutoStore is that it is not restricted to one size or form," Says Bill Leber, Director of Business Development & Marketing for Swisslog. "The system can easily be adapted to fit different building heights, span multiple levels and even surround obstacles in the warehouse, such a pillars or walls. The various restrictions of Komplett's existing building posed no difficulty for the new system."
"Since AutoStore consists of several modules that operate independently of each other, there is no single point of failure," Leber explains. "Should, for example, one of Komplett's robots need maintenance, then its tasks will automatically be taken over by other robots deployed in the system."
"If Komplett needs to increase capacity, it is very easy to extend the number of robots and increase the number of picking stations," Leber continues. "It is also rather easy to extend the grid itself and add more bins, with no negative impact to ongoing operations. It is very flexible in terms if scalability."
Another flexibility of the system is that it automatically optimizes the storage position of goods in the grid by keeping the more frequently requested products higher up for faster access times.
DC Flow
"AutoStore is the critical automation in our DC, but it functions as one module in our total system," says Vindegg. "When we introduced AutoStore, we also installed 1,200 linear feet of conveyor and a shipping sortation system. We put a lot of effort into the inbound and outbound material flow."
"From receiving inbound, we register that we have received the products," continues Vindegg. "Then we put the majority of our items into locations in AutoStore, for the small items, and into racks for bigger items like flat screen TVs, PCs and laptops. We have about 5,000 pallet locations, a racking system for buffer store, and 28 pick stations that we use for both inbound and outbound. Eighty percent of our product moves through AutoStore."
When a robot delivers a bin to a pick station, the worker picks the required number of units and the robot returns it back to storage. The new bins are thereby delivered back-to-back and the operator rarely has to wait for bins. Komplett's AutoStore system can hold approximately 700 live picking tasks in its queue at any one time. There is an operator HMI panel on every pick station that shows pick status information. The total performance of the system can be controlled by a number of different parameters.
From the AutoStore pick stations, the orders are packed in boxes, which are conveyed away from the picking stations, automatically labeled, and conveyed through a shipping sorter to the 15 shipping gates.
30 Percent Increase in Efficiency
"We like the idea that the system will reconfigure the position of SKUs based on those used most," explains Vindegg. "AutoStore always picks from the top, so if we have to use one bin very often it will just stay on the top. And the bins that we very seldom need sink to the bottom. Our statistics show that 90 to 95 percent of what we pick most often is in the three upper layers. That gives us automatically more efficiency."
"Since we completed the automation, our man-hours have reduced, and our volume of orders have increased," says Vindegg. "We switched people from pick-and-pack to receiving because the automation increased the workload in the receiving area. What we look at is the productivity for the total warehouse, and we show a 30 percent efficiency increase for the entire DC operation. That is based on counting orders per spent man hours. Man-hours have reduced, compared to the number of orders which have increased. That is a very important key performance indicator for us."
About Swisslog
Swisslog (www.swisslog.com ) is a global provider of integrated logistics solutions for warehouses, distribution centers and hospitals. Its comprehensive services portfolio ranges from building complex warehouses and distribution centers to implementing Swisslog's own software to intra-company logistics solutions for hospitals. Swisslog's solutions optimize customers' production, logistics and distribution processes in order to increase flexibility, responsiveness and quality of service while minimizing logistics costs. With years of experience in the development and implementation of integrated logistics solutions, Swisslog provides the expertise that customers in more than 50 countries around the world rely on.
With North American operations located in Newport News, Virginia and Global Headquarters in Buchs/Aarau, Switzerland, Swisslog currently employs over 2,000 staff in 20 countries worldwide.
For more information on Swisslog Warehouse & Distribution Solutions contact Bill Leber, Director of Business Development & Marketing; 161 Enterprise Drive, Newport News, VA 23603; Phone 757-820-3400: email bill.leber@swisslog.com; www.swisslog.com
To reach Komplett ASA