The Changing Needs Of Maintenance In High-Speed Distribution Centers - Resident Maintenance Programs Gaining Popularity In Highly Automated DCs
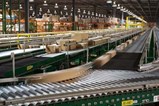
By Jim McMahon, Dematic Corp.
There is clearly a change afoot with the management of maintenance functions in automated distribution centers, and particularly those DCs with high-speed, high-throughput equipment. Where once material handling equipment maintenance was done almost exclusively with in-house maintenance staff, today's highly automated DCs are now causing a gradual shift to the use of outsourced resident contractors.
Automated distribution centers, traditionally, have hired maintenance contractors and temporary employees to carry out work for peak and specialized services. The concept of outsourcing, however, represents a long-term, results-orientated relationship with a specialized outside company, which is performing turnkey maintenance functions that traditionally were done by the DC's inside staff.
Resident maintenance programs provide its client DCs with on-site mechanical and/or electrical technicians who perform preventive, corrective and emergency maintenance, as well as operational assistance to ensure the material handling system functions at optimum efficiency. These programs have proven effective at increasing performance and prolonging the life cycle of automated, high-performance DCs.
There are several reasons influencing this change to resident maintenance programs in automated DCs. The most critical is the desire to optimize system uptime, which requires a more comprehensive and systematized approach to maintenance than what is typically in place in many DCs. Additionally, as equipment becomes more automated and therefore sophisticated, the need for more technically specialized personnel, which the DC would not necessarily have on staff, becomes a factor. Another factor influencing the change to resident maintenance programs is senior management's increased initiatives for distribution centers to become more accountable for key performance indicators (KPIs), and subsequently function as more cost-efficient operations. Finally, there is the desire to maximally extend the life of the distribution center's capital equipment to reduce cost of ownership for the DC.
Maintenance Staffing Challenges
Ten years ago, material handling systems in distribution centers were mostly mechanically based. There is still a strong mechanical component, but high-speed, automated systems are much more dependent upon controls and software that are critically important to the performance of these systems. Distribution centers run at a higher level of precision than ever before, with increased system complexity, requiring software and automation technicians with new skill sets.
Even non-specialized personnel require more extensive training on the high controls content equipment – such as operating an AS/RS (Automated Storage and Retrieval System) – than with the mechanical-based DCs. This has ushered in a new set of staffing problems for automated DCs. According to Rider & Associates, a supply chain consulting firm, a typical automated distribution center will experience employee turnover rates of between 50 and 60 percent per year. Employee turnover is expensive, with costs typically averaging 25 percent of a worker's annual salary. These costs factor in recruiting, selection, training and lost productivity expenses.
If the DC's automated system was installed more than three years ago, there is a high probability that no personnel remain that were there during the initial equipment training. Keeping the personnel trained on the material handling equipment has effectively become a continual process for DC managers.
Higher Expectations for System Uptime and Longevity
The primary reason to perform maintenance on a DC's equipment is to prevent costly, unplanned shutdowns, and also to maximize the life of the equipment. There is little worse in a distribution center than a cessation of throughput because of equipment failure, especially when it could have been avoided with proper maintenance. The costs of the equipment repair and the lost employee time are marginal compared to the loss of throughput, which in a high-volume DC could be as high as 200,000 cases per day not processed because of a shutdown.
Corporations are increasingly viewing their DC operations from a performance versus cost standpoint. Establishment and monitoring of key performance indicators (KPIs) for maintenance, safety and system uptime within the distribution environment has taken on a whole new perspective with an eye toward maximum output, optimum equipment utilization and system longevity. Such metrics are monitored on a daily scorecard and used to measure current DC performance, and to plan and adjust for future operations. The implementation of measurable KPIs for best practices and safety, security, and compliance regulations, as well as complex maintenance, repair, and overhaul (MRO) strategies is a structural component of resident maintenance programs.
There are still many DCs, though, that run their maintenance on the basis of "Don't fix it until it breaks". They will reduce the maintenance staff and run the system until it tears apart and breaks down, then they fix it, and run it again until it breaks down, continuing this cycle over and over. This saves initially on reduced maintenance manning and short-term spare part costs, but it negatively impacts the DC with unscheduled and uncertain stoppages and reduced system longevity.
Of critical importance is locating ahead of time problems and inefficiencies that would lead to reduced performance and degenerative operation, as well as scheduling proper preventative maintenance routines. Running a high volume of cartons through a DC at high velocity creates increased wear and vector stresses on the system. As the speed increases, the force increases as well on the mechanical structures of the system. These wearing forces can go unrecognized by a DC's operational staff until the system's throughput slows or begins to break down. This criteria itself is frequently the degenerating maintenance variable most missing with DC facility managers.
Without retrofit or equipment replacement, as a high-volume DC's equipment ages its performance expectations diminish. The standard life of conveying equipment that is running at high speed for 15 hours a day without proper maintenance is roughly a seven-year life span. After that period, conveyors and sortation equipment typically have to be retrofitted before lessened performance becomes a significant issue.
But high-volume, highly-automated conveying and sortation equipment can be maintained to run efficiently for much longer periods of time before the need for upgrade, and thereby reducing the total cost of ownership. It is not unusual for high-speed material handling systems to run for more than a dozen years in operation and still be going at 100 percent functionality. This necessitates, however, a very organized and comprehensive protocol at providing preventative, corrective and emergency maintenance on the equipment, a regimen that few distribution centers perform adequately.
The median uptime for highly-automated DCs is in the 93 – 94 percent range. This is no match for distribution centers running rigorous pro-active resident maintenance campaigns with uptimes of 98 – 99 percent-plus. Resident maintenance programs have proved extremely successful with increasing uptime, reducing the need for costly spare parts and significantly extending the life of DC systems, and ultimately reducing capital expenditures for new equipment.
Profile of a Top-Tier DC Resident Maintenance Program
One of these programs is Dematic's Resident Maintenance Program. Dematic is the largest manufacturer of material handling equipment in the world, with many high-speed, high-volume DCs using its Resident Maintenance Program. A closer look at how its program is set up would present a clear insight into the functionality of these programs at a top-tier level.
Completely opposite to the "Don't fix it until it breaks" maintenance mode, is Dematic's multi-layered approach to pro-active maintenance. The multiplicity of the program's scheduled maintenance procedures and performance indexes cover every aspect of a functioning distribution center. The program integrates: (a) maintenance techniques and methodologies for state-of-the-art preventive maintenance; (b) a protocol for continuous improvements to be made on the system; (c) a predictive maintenance regimen; (d) determination and management of maintenance key performance indicators; (e) monitoring of crucial maintenance strategy elements such as spare parts management and control, maintenance control systems, documentation systems, administrative structures and maintenance team structures; (f) failure modes and effects analysis; and (g) corrective and troubleshooting maintenance actions. These overlapping functions ensure optimal operation of the material handling system and maximum system life.
Not all resident maintenance programs are alike. Each has characteristics which give it a unique approach to resident maintenance. Because Dematic is both an equipment integrator and manufacturer, it brings an OEM engineering insight into the mechanics of its installed operating systems as well as individual equipment functionality. The company has a huge installed base of its equipment within distribution centers, and it keeps all of this information available in database format on every system. Technicians can access and evaluate any system's complete service history and makeup.
Dematic also maintains best practice libraries encompassing the company's entire installed base. It continually tracks maintenance trends developing in any service area of its systems, through database entries. This allows its technicians to uncover and identify potential issues with a system even before they arise, and can be addressed with preventive maintenance, if required. When corrected at an early stage, it prevents the need for emergency corrective maintenance later which could influence the uptime of the system. The result is savings in both time and money for the distribution center.
"Having technicians that are equipped with a strong general knowledge of material handling systems, as well as those possessing specialized skills in particular technical areas like software and automation operation is critical," says J. Scott Filgis, a resident maintenance site manager with Dematic. "This means that service personnel will understand the intricacies of any system's problem, and will be able to provide a solution that fits into the scope of each customer's operation, whether it is Dematic's equipment or another material handling system. Also, because most of our clients have Dematic systems, when we have a more complex system problem we have direct access to the people that initially commissioned the project, such as the engineers that designed it or the technicians that installed it."
"Resident maintenance functions encompass everything from mechanical to IT items," explains Filgis. "Replacing bearings in rollers, handling motors and reducers, electrical troubleshooting, changing the timing of diverts, troubleshooting variable frequency drives and reprogramming software. We also modify the system to enhance it, should a client request this service. If our client decides they want a different kind of functionality, then we can build that function into their system on site."
The system uses a maintenance and asset management software program that schedules all preventative maintenance, tracks breakdown maintenance and keeps inventory control of spare parts. It organizes and tracks equipment inventories, schedules preventative maintenance tasks, tracks motor run times, manages equipment costs, tracks equipment history, maintains labor records, generates work orders and a host of other reports.
When a system has a problem, defining where the problem lies can be a challenge. Dematic uses a graphic visualization program to tell technicians exactly where the problem is located. System manuals, including all of the parts for the equipment, are displayed on the visualization. It is a very efficient resource to identify where the problems are located and finding the right part to resolve it.
The Dematic maintenance technicians also provide hands-on training to its client's operational staff. As DC personnel change frequently, this is usually an on-going program.
As a complement to its resident maintenance program for material handling systems, Dematic also provides resident facility maintenance, handling functions like dock locks, lighting, heating and ventilation. Once maintenance technicians are permanently on site servicing the material handling system, many DCs see it as a natural and efficient move to leverage these assets for facility maintenance, which is indeed a growing trend within the more highly automated distribution centers.
Exel's 99 Percent Uptime
One company that supports vigorous pro-active maintenance initiatives, and has partnered with Dematic on its resident maintenance program for one of its high-speed DCs, is Exel, Inc., which operates 99 million square feet of distribution space in the Americas.
Operating more efficiently with DC employee retention than industry norms – Exel's DC turnover rate is approximately 30 percent annually, compared to industry averages of twice that number – the company's resident maintenance focus has been on improving system uptime and extending the system's life.
"Our goal of 98 percent uptime is a high standard from an engineering standpoint," says Steve Nissen, Director of Operations for Exel's Groveport, Ohio, DC. "Dematic's resident maintenance crew concentrates on maximizing our system's uptime, which is running very high in the 99.4 to 99.8 percent range. The program is very focused on preventative maintenance."
"Exel looks at a company's ability to work with different types of technologies and solutions," continues Nissen. "When you get to the much more integrated technology solutions where there is a heavy amount of automation, you really want to be sure the people you have on staff, or those that you contract in, are completely capable of troubleshooting and servicing that equipment."
"With the very large automated solutions we certainly want to maximize the up-time of our investment with a heavy focus on predictive and preventive maintenance strategies, and spare parts," explains Nissen.
Maximizing a DC's Performance
"Such a program has tremendous flexibility," says Steven Brandt, Dematic's Business Development Manager for its Resident Maintenance Programs. "It can be customized depending on the sophistication of the material handling system, or on the location. It can be customized to accommodate different operational schedules – for example, some clients might run 20 hours per day, seven days a week, others might run one shift five days a week. The program can be customized to accommodate a busy season where there would be a need increased staffing. It can be customized to focus just on the maintenance of the material handling system, or, it may include the DC management or even the duties of facility-type maintenance. Or, it can be customized to include different skill sets for technicians.
Each distribution center has its own unique needs, for which Dematic develops a custom resident maintenance program to meet those needs, whether it is Dematic equipment being serviced or any third-party equipment."
"The results so far have been very favorable," continues Brandt. "We have had a very high renewal for our resident maintenance sites. But the number one thing we strive for is achieving the highest uptime possible. That means the system is running, with no unexpected system downs due to maintenance issues. We like to achieve an uptime of at least a 98 percent, but we have some clients that are achieving 99 percent-plus."
A well structured resident maintenance program can yield huge benefits for a distribution facility, such as: (a) flexible staffing as operational requirements change for peak seasons; (b) optimized uptime; (c) cost reductions through increased productivity and reduction in overall system maintenance costs; (d) dedicated maintenance staffing resources focusing on the material handling system; (e) improved equipment safety because of regular maintenance; (f) reduced parts consumption due to maximization of equipment life spans; (g) increased equipment longevity - a well prepared and executed maintenance program reduces the possibility of emergency or unscheduled maintenance and provides investment protection. Each of these help reduce the cost of ownership.
Not all distribution centers have automated systems. But for those that do, the focus on a comprehensive predictive maintenance strategy is critical to a truly efficient operating facility. But even better, a well-prepared and properly staffed resident maintenance program provides the highest possibility to optimize a distribution center's performance.
About Dematic Corp.
Based on a rich tradition of over 70 years of worldwide industry expertise in creating logistics results and more than 10,000 systems installed worldwide, Dematic Corp is the world's leading supplier of logistics automation solutions, systems and service.
Beginning with Rapistan's rich history from gravity conveyors to automated, modular conveyor and sortation solutions, Dematic now offers a full range of engineered and highly configurable system solutions that optimize warehousing and distribution operations. With Dematic, companies can reduce distribution costs, maximize overall logistics efficiencies, and increase the operating speed of their supply chain.
Dematic is a global company with operations in 22 countries around the world. Its North American headquarters is located in Grand Rapids, Michigan. For more information, visit www.dematic.us.
SOURCE: Dematic Corp.